The pharmaceutical and medicinal industry is responsible for the production of life-saving medications and therapeutic products. When it comes to production, ensuring the consistency, potency, and quality of these products is essential. One critical step in the production process is homogenization. Here are six crucial considerations when selecting a homogenizer for pharmaceutical manufacturing:
1. Particle Size Reduction: The size of particles can greatly influence the potency, efficacy, and stability of pharmaceutical products. A homogenizer should be efficient in reducing and uniformly distributing particle sizes.
2. Pressure Range: Given that different formulations require different pressures, it’s essential to select a homogenizer with a versatile pressure range.
3. Sanitation and Sterilization: The homogenizer should be easy to clean and sterilize to prevent any contamination, ensuring the safety and efficacy of the end product.
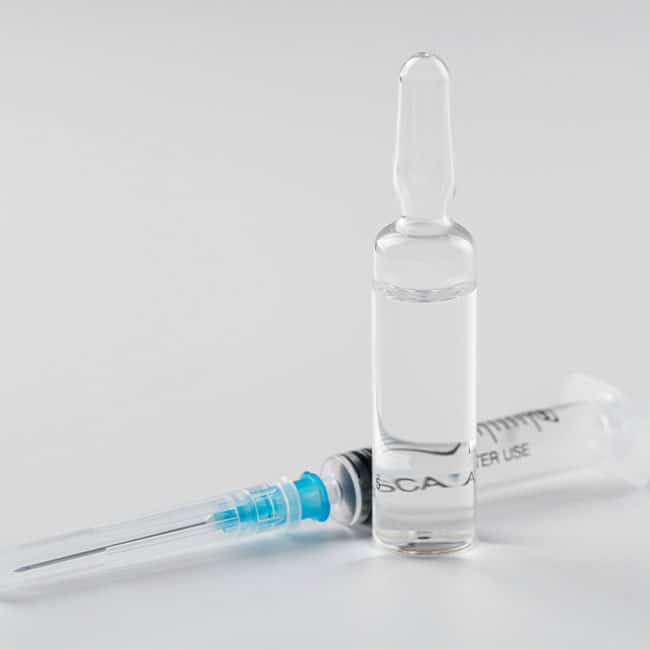
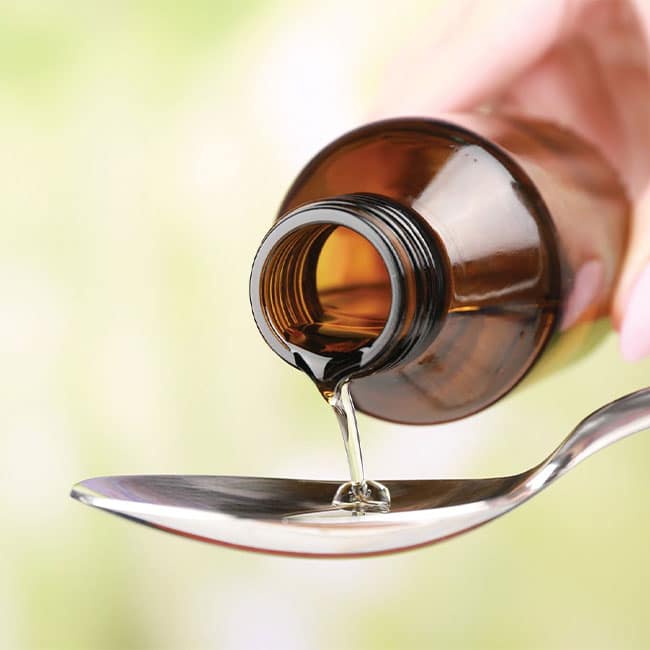
4. Scalability: As demands change, the production capacity might need to be scaled up or down. The chosen equipment should be adaptable to different production scales without compromising quality.
5. Material Integrity: The homogenizer should be made of materials that won’t react with or contaminate the product being processed.
6. Operational Safety: Given the high pressures involved, it’s essential to ensure that the homogenizer is designed with safety measures to protect the operators and the surrounding environment.
Hommak Homogenizers: A Benchmark of Success in the Pharmaceutical Sector
When talking about pioneering success in the pharmaceutical industry, Hommak homogenizers stand out. These are not just machines but finely-tuned instruments, meticulously designed for precision and efficiency.
The homogenization process involves pumping an emulsion, suspension, or solution into a high-pressure homogenizer. This mixture is then forced through a specialized homogenization valve under incredibly high pressures, reaching up to 1,500 bar or 21,750 PSI. As particles, with a maximum size of 500 µm, enter the homogenizer, they undergo a transformation. Larger particles are dispersed, and their sizes are significantly reduced. The resulting particle size, depending on the specific application, typically ranges between 0.4 to 1 micron.
Hommak homogenizers deliver consistent results, ensuring that the quality and potency of the pharmaceutical products remain uniform throughout the batch. This uniformity is vital in maintaining the efficacy and safety of the medications.
Furthermore, the technology employed by Hommak allows for the optimization of formulations. By achieving such small particle sizes, there’s an increase in the surface area of active ingredients. This can enhance the bioavailability of many pharmaceutical products, making treatments more effective and reducing potential side effects.
In conclusion, when seeking excellence in pharmaceutical manufacturing, it’s not just about selecting the right homogenizer but about choosing a reliable partner. Hommak homogenizers have proven to be a trusted companion for many pharmaceutical companies, ensuring top-tier quality and unmatched consistency.