The pharmaceutical landscape is continuously evolving, with innovative technologies playing a pivotal role in advancing drug development and manufacturing. Among these technologies, the homogenizer stands out as a crucial instrument, particularly in the field of vaccine production. This blog post delves into the five significant contributions of homogenizers in the vaccine manufacturing process within the pharmaceutical industry.
1. Enhanced Stability and Consistency
One of the primary contributions of homogenization in vaccine production is the enhancement of stability and consistency. Vaccines often contain a blend of different substances, including antigens, adjuvants, and stabilizers. Homogenizers efficiently mix these components at a microscopic level, ensuring a uniform distribution. This uniformity is critical for the stability of the vaccine, as it prevents the separation of components over time, thereby maintaining its efficacy from the first dose to the last.
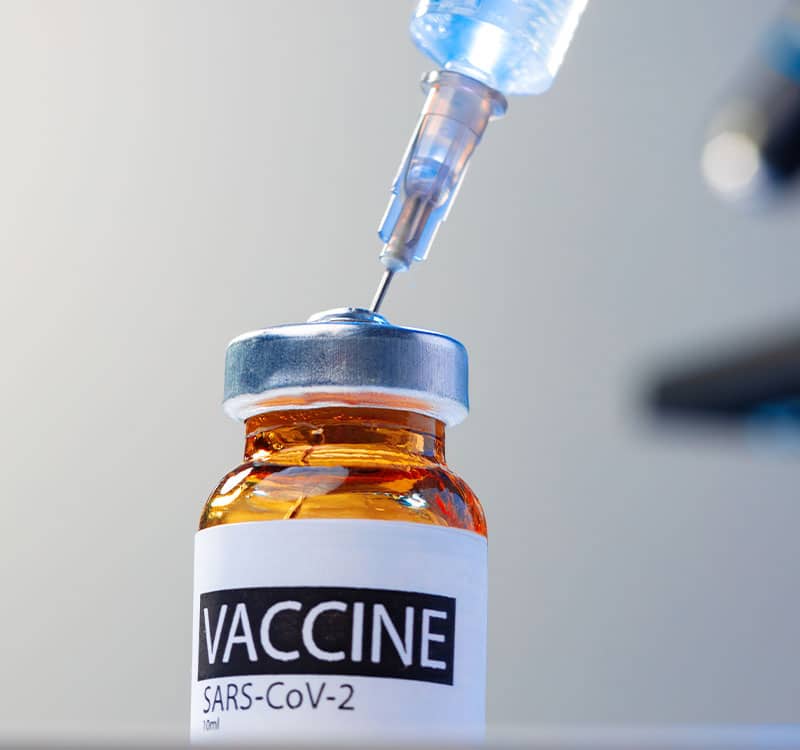
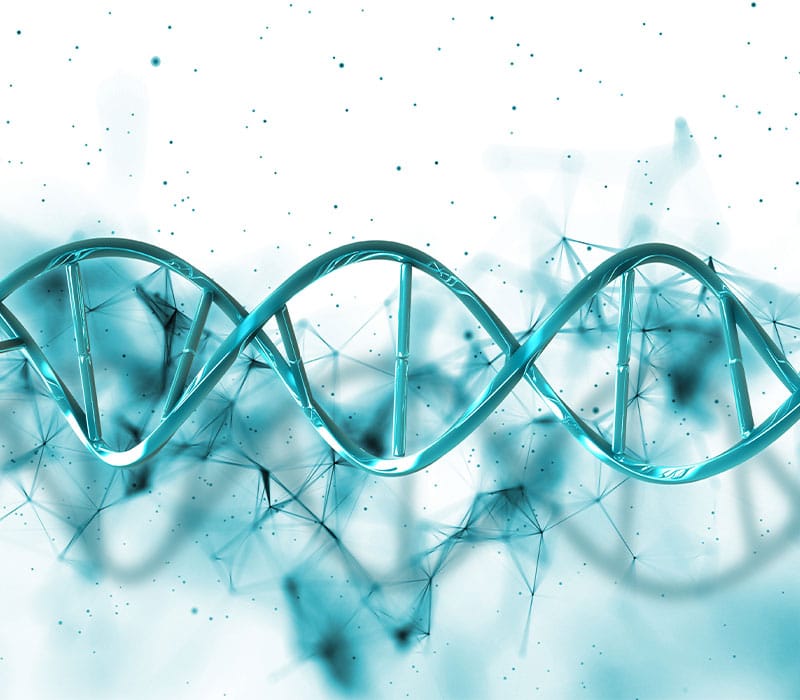
2. Improved Bioavailability
Bioavailability, or the rate and extent to which an active ingredient is absorbed and becomes available at the site of action, is a critical factor in vaccine effectiveness. Through the process of high-pressure homogenization, vaccines can achieve a finer particle size, enhancing the surface area for interaction with the immune system. This increased surface area can lead to a more robust and rapid immune response, thereby improving the vaccine’s overall effectiveness.
3. Scalability for Mass Production
The global demand for vaccines, especially highlighted during the COVID-19 pandemic, underscores the need for scalable production methods. Homogenizers are instrumental in this aspect. They are designed to handle a range of volumes, from small-scale laboratory production to large-scale industrial manufacturing. This scalability ensures that vaccine production can be ramped up quickly and efficiently, meeting urgent global health needs.
4. Quality Control and Reproducibility
Maintaining a high standard of quality is paramount in pharmaceutical manufacturing. Homogenizers contribute significantly to quality control by ensuring the reproducibility of vaccine batches. The precision and control offered by modern homogenizers mean that each batch of vaccine can be produced with consistent quality, meeting stringent regulatory standards. This reproducibility is crucial not only for the effectiveness of the vaccine but also for building public trust in vaccination programs.
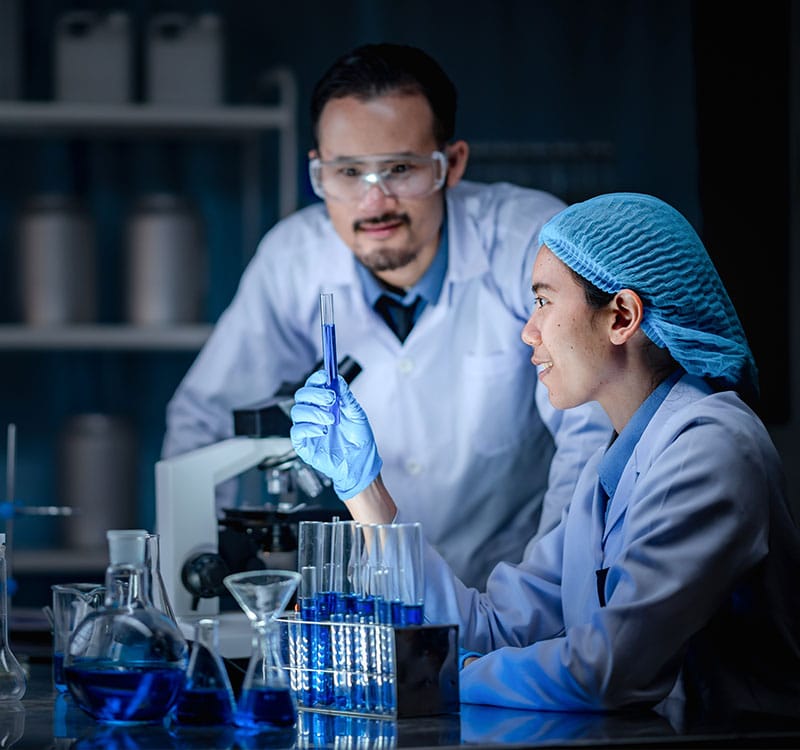
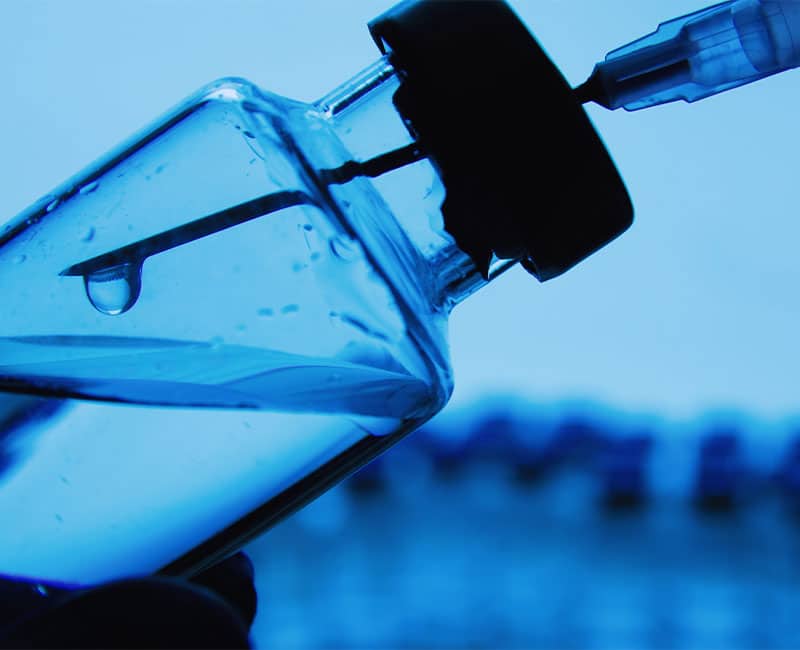
5. Innovative Vaccine Development
Lastly, homogenizers play a pivotal role in the development of new and innovative vaccines. As vaccine technology advances, including mRNA-based vaccines and nanoparticle carriers, the need for advanced homogenization techniques becomes more evident. Homogenizers can assist in the development of these novel vaccines by facilitating the creation of nanoemulsions and liposomes, which are crucial for the delivery of these new types of vaccines.
Conclusion
In conclusion, the homogenizer is much more than just a piece of equipment in the pharmaceutical industry; it is a catalyst for innovation and efficiency in vaccine production. Its contributions to stability, bioavailability, scalability, quality control, and innovative development have established it as an indispensable tool in the quest to combat infectious diseases globally. As we continue to face new health challenges, the role of homogenization in vaccine production will undoubtedly remain at the forefront of pharmaceutical technology and innovation.