Homogenization is a unique method applied to fluid products with a heterogeneous or non-homogeneous composition. This process involves passing these substances through a narrow gap under intense pressure. The high-speed passage results in the micronization of the particles, expanding their surface area. As a result, a permanent homogeneity within the mixture is achieved. This scientific procedure is commonly known as “homogenization.” The specialized machine that facilitates this transformative process is called a “homogenizer.”
What is Homogenization?
Over 20 years of experience
More than 3500 references worldwide
Superior quality and Competitive pricing
Get in Touch!
Homogenizer Working Principle
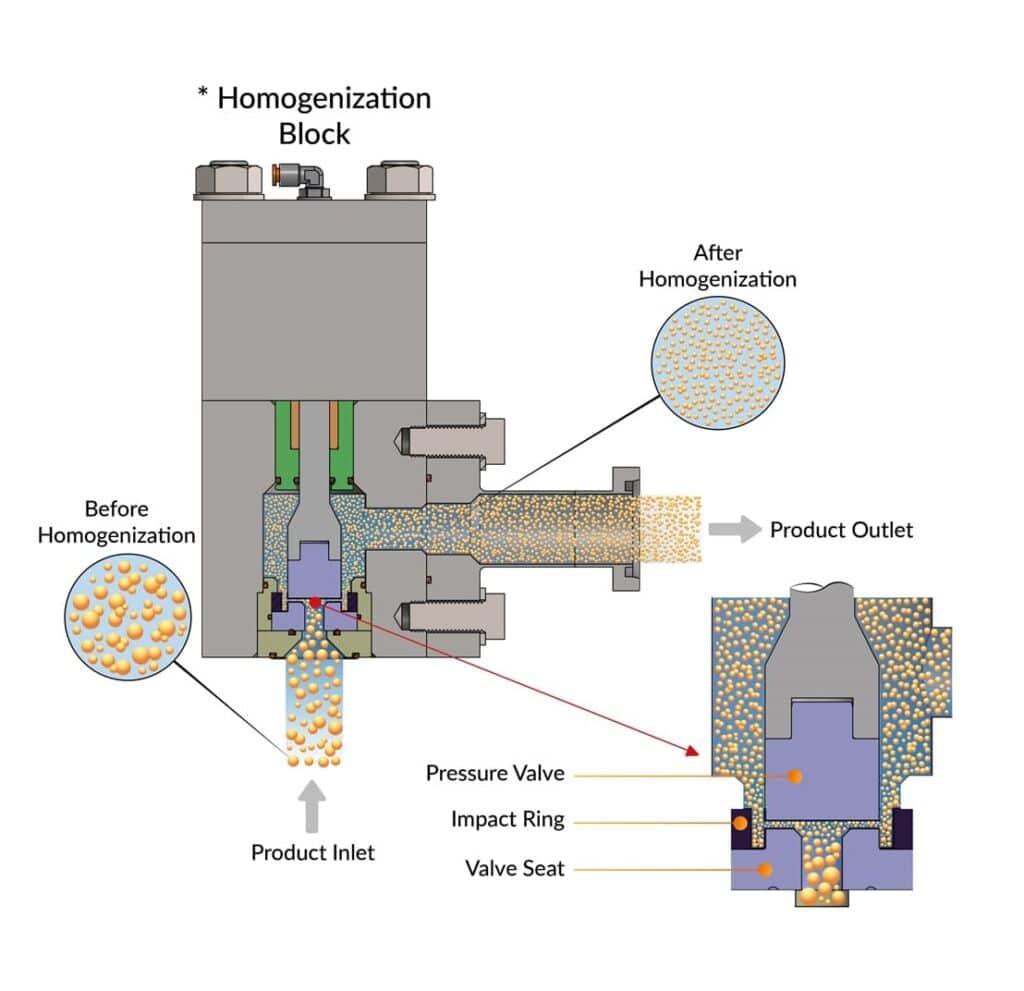
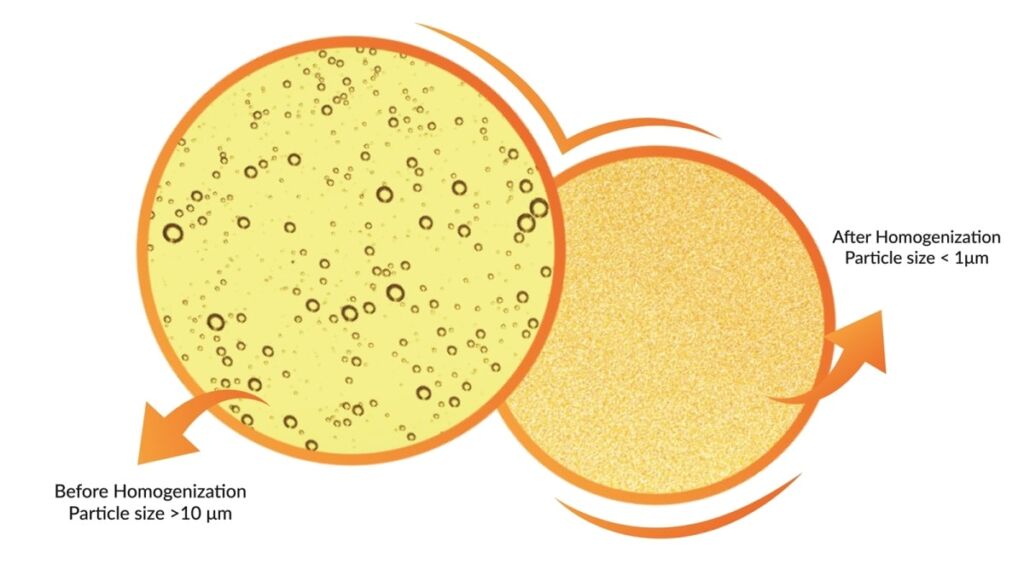
Advantages of Using Homogenizers
- Prevents sedimentation in fluid products
- Brings the products to the desired viscosity values
- Adds value by improving the properties of the products
- Improves the taste and texture of drinks
- Provides high-quality color characteristics
- It makes the milk appear whiter
- Facilitates digestion as it increases the surface area of food and beverages
- Improves the consistency of creams and lotions
- Decreases the need for additives
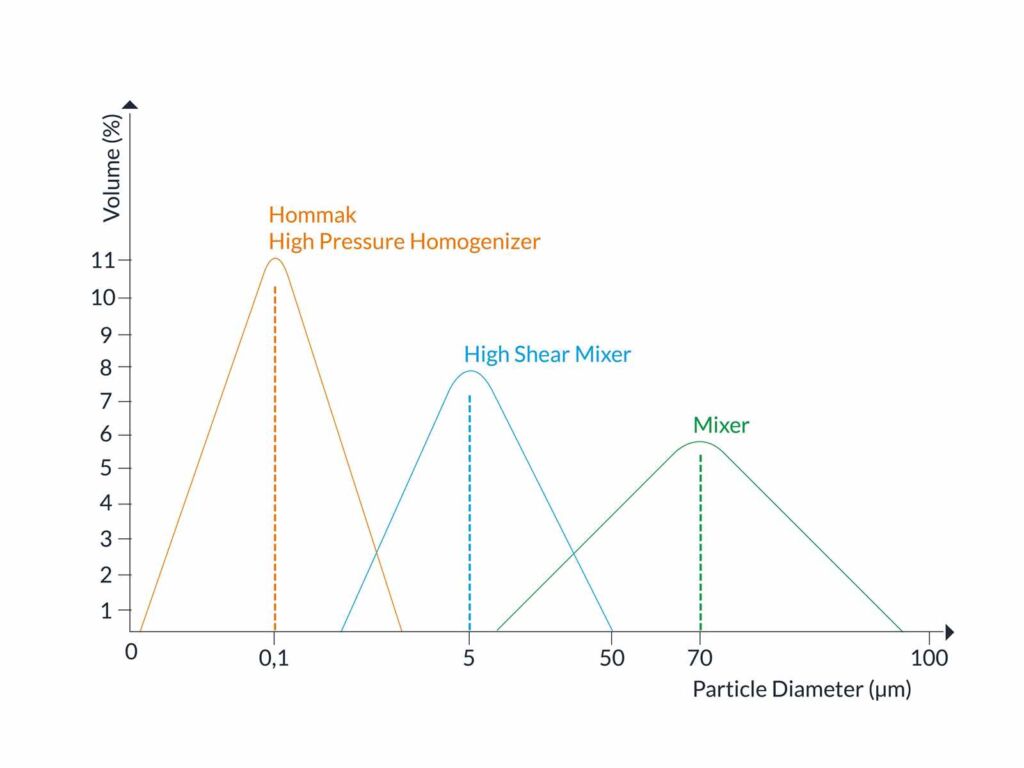
Hommak offers high-level customer satisfaction with its high-quality products that meet customer needs. As a result of years of experience and R&D studies, HOMMAK manufactures homogenizers that can work with lower energy consumption and the necessary optimizations.
Homogenizing Valve
- Unique homogenizing valve structures
- Zirconium ceramic, silicon nitride ceramic, tungsten carbide, and cobalt carbide Materials
Frame
- Unique homogenizing valve structures
- Zirconium ceramic, silicon nitride ceramic, tungsten carbide, and cobalt carbide Materials
Gearbox
- Resin reinforced nodular cast iron material
- Vibrationless and high strength structure
- Use of reducer in all homogenizers except L series
Suction and Delivery Check Valves
- Unique mushroom and ball check valve structures
- Production with cobalt carbide alloy and tungsten carbide alloy material
- Check valve seat for double-sided use
Plungers
- High strength special stainless steel and zirconium ceramic material
- Surfaces appropriate for the usage area; chrome, cobalt carbide, tungsten carbide, and ceramic coating applications
Sealing Components
- Use of hygienic felt in accordance with food standards
- Longer working performance with lower RPM
- Kevlar, PEEK, Zedex, TIVAR, POM, PE, FKM, PTFE materials
Compression Head
- Hommak special MonoBlock and MultiBlock design
- Reducing the surface for microorganism to attach, with nonblind-spot design
- Surface Roughness: Ra <1.6μm, Ra <0.8μm, Ra <0.5μm (electropolished)
- Usage of FEM stress analysis in design
- Easy felt and check valve replacement
- 10-year MonoBlock warranty against crackings
Related Products
Industrial Homogenizer
HOMMAK Homogenizers are manufactured by selecting the valve design and material to meet the needs of the sector in which it will be used.
Laboratory Homogenizer
HOMMAK laboratory type homogenizer has a portative and transportable structure. It enables you to improve your current products, test the effect of homogenization on products, and get optimum results by determining the best process parameters.
High Pressure Piston Pump
High-pressure pumps are ideal for transferring high density and viscosity products. It is used as the feeder for the tower in the production of milk powder, food powders, chemical powders, and other powder types.
Pilot Plant Homogenizer
HOMMAK pilot plant homogenizers are designed for limited production and R&D studies.
High Shear Mixer
HOMMAK Makine developed the Hommix Powder-Liquid Blender as a result of long R&D studies.
High Pressure Homogenizer
Fluid products in heterogeneous (non-homogeneous) structures pass through the narrow gap under high pressure.
Ricotta System
It is an innovative solution designed for the sector and the need and is the invention of HOMMAK.
Pasteurizer
Our plate pasteurisation and sterilisation systems are designed in a manner which you can safely use in the pasteurisation processes
Yogurt Filling Machine
It is designed to allow you to fill yogurt in the desired volume or weight, with 0.1% precision and high speed.