Innovative production systems and turnkey projects are revolutionizing how we formulate skincare products. High Shear Mixers, a critical player in this transition, grant cosmetic manufacturers unprecedented control over their product’s quality, consistency, and efficiency. Today, we delve into the transformative world of homogenization and explore the key advantages of High Shear Mixers in skincare production.
Skincare products include a vast range of lotions, gels, creams, and more. The core composition encompasses alcohol, cream, wax, and approximately 50% water. One of the primary production goals is to decrease the particle size, consequently augmenting the product’s viscosity, which in turn enhances its quality and feel on the skin.
Key Advantages of High Shear Mixers in Skincare Production
High Shear Mixers, celebrated for their homogenizing abilities, lead the way in this process. They present unique benefits, with notable advantages being:
-
80% energy conservation,
-
80% decrease in process time,
-
It provides more homogenized products and improves product quality.
- Enhanced Texture and Consistency: High Shear Mixers are adept at creating a smooth and homogeneous texture. The homogenization process reduces the particle size, thereby improving the product’s viscosity. This results in a more stable product that feels smoother on the skin.
- Improved Quality: The use of a High Shear Mixer facilitates high-quality production without necessitating additional active components. This mixer creates an appealing viscosity through high-pressure homogenization alone, preserving the integrity of the recipe and the product’s overall quality.
- Increased Efficiency: High Shear Mixers have demonstrated superior efficiency compared to competing machines. They allow for a significant viscosity increase, even when the product is run twice through the homogenizer under the same pressure.
- Advantages of Powder-Liquid and Liquid-Liquid Mixers: These mixers can operate at both high and low temperatures, allowing processing of high viscosity products. Maintenance is simple, with easily changeable seals and a straightforward cleaning process. They offer custom designs based on your requirements and use conditions. An additional pump is unnecessary, and their installation is simple. These mixers boast an ergonomic design and low maintenance costs.
- Cost-Effective: High Shear Mixers can be more cost-effective over time since they don’t require additional active components to increase viscosity. They optimize the use of ingredients, thereby saving costs and improving profitability.
- Advanced Production Capabilities: High Shear Mixers can operate efficiently at room temperature and under varying pressures, providing flexibility during production. This adaptability enables manufacturers to experiment with different product characteristics without compromising efficiency or quality.
- Energy and Time Efficient: Compared to traditional methods, these mixers offer an 80% reduction in both energy usage and process time, resulting in more homogenized products and improved product quality.
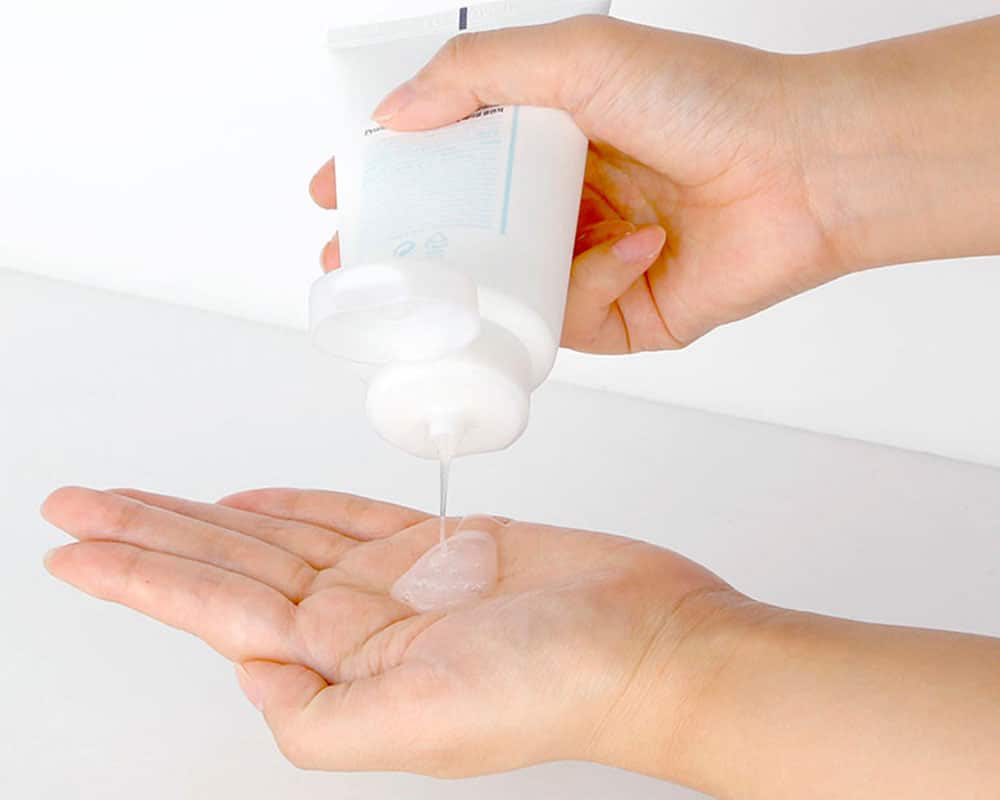
Conclusion:
High Shear Mixers are a game-changer in skincare production, enabling manufacturers to create superior products while maintaining efficiency and cost-effectiveness. The era of homogenization has dawned, setting a new standard of quality in the skincare industry.
For further insights on innovative production systems, turnkey projects, and the latest in homogenization technology, stay tuned to our blog.